The Production Process of Mainstream Current Sensing Resistors
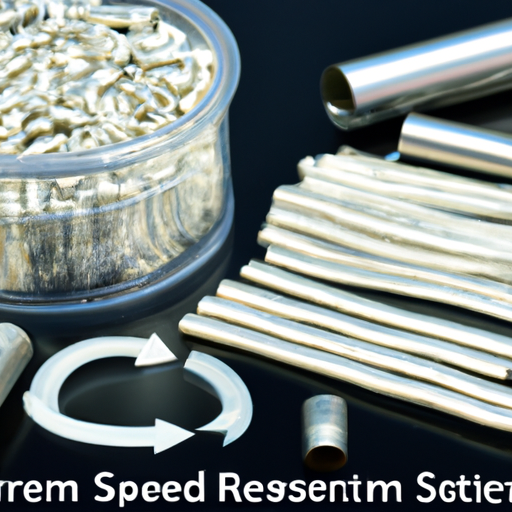
I. Introduction
A. Definition of Current Sensing Resistors
Current sensing resistors, often referred to as shunt resistors, are critical components in electronic circuits that measure the flow of electric current. By providing a known resistance, these resistors allow for the calculation of current based on the voltage drop across them, following Ohm's Law (V = IR). This functionality is essential in various applications, including power management, battery monitoring, and motor control.
B. Importance in Electronic Circuits
In modern electronics, the ability to accurately measure current is vital for system efficiency and safety. Current sensing resistors play a crucial role in protecting circuits from overcurrent conditions, enabling feedback mechanisms in power supplies, and ensuring optimal performance in battery-operated devices. Their reliability and precision directly impact the overall performance of electronic systems.
C. Overview of the Production Process
The production of current sensing resistors involves several stages, from raw material selection to final testing and packaging. Each step is critical to ensure that the resistors meet the required electrical and mechanical specifications. This blog post will delve into the various aspects of the production process, highlighting the importance of quality and innovation in this field.
II. Types of Current Sensing Resistors
A. Shunt Resistors
Shunt resistors are the most common type of current sensing resistors. They are typically low-resistance components placed in series with the load to measure current flow. Their design minimizes power loss while providing accurate current readings.
B. Wirewound Resistors
Wirewound resistors are constructed by winding a metal wire around a ceramic or fiberglass core. This design allows for high power ratings and excellent thermal stability, making them suitable for high-current applications.
C. Thin Film Resistors
Thin film resistors are made by depositing a thin layer of resistive material onto a substrate. They offer high precision and stability, making them ideal for applications requiring tight tolerances.
D. Thick Film Resistors
Thick film resistors are produced by printing a paste of resistive material onto a substrate and then firing it at high temperatures. They are cost-effective and widely used in various applications, though they may not offer the same precision as thin film resistors.
E. Comparison of Types
Each type of current sensing resistor has its advantages and disadvantages, depending on the application requirements. Shunt resistors are favored for their simplicity and low cost, while thin film resistors are preferred for high-precision applications. Understanding these differences is crucial for selecting the right resistor for a specific application.
III. Raw Materials
A. Conductive Materials
1. Metal Alloys
The choice of conductive materials is critical in the production of current sensing resistors. Metal alloys, such as nickel-chrome or copper-nickel, are commonly used due to their stable resistance characteristics and good thermal properties.
2. Carbon Composition
Carbon composition materials are also used, particularly in applications where high power ratings are required. They offer good thermal stability and are less susceptible to temperature variations.
B. Substrates
1. Ceramic
Ceramic substrates are often used for their excellent thermal conductivity and electrical insulation properties. They provide a stable base for resistive materials and help dissipate heat effectively.
2. Epoxy
Epoxy substrates are another option, particularly for thick film resistors. They are lightweight and can be molded into various shapes, making them versatile for different applications.
C. Coatings and Insulators
Coatings and insulators are applied to protect the resistors from environmental factors and to enhance their performance. These materials help prevent moisture ingress and improve the overall durability of the resistors.
IV. Design and Engineering
A. Electrical Specifications
1. Resistance Value
The resistance value is a critical parameter that determines the current sensing capability of the resistor. Engineers must carefully calculate the desired resistance based on the application requirements.
2. Tolerance
Tolerance indicates the allowable deviation from the specified resistance value. High-precision applications require resistors with tight tolerances to ensure accurate measurements.
3. Temperature Coefficient
The temperature coefficient measures how much the resistance changes with temperature. A low temperature coefficient is desirable for applications where temperature fluctuations are expected.
B. Mechanical Specifications
1. Size and Form Factor
The size and form factor of current sensing resistors are essential for integration into electronic circuits. Designers must consider the available space and the thermal management requirements when selecting resistor dimensions.
2. Power Rating
Power rating indicates the maximum power the resistor can handle without overheating. This specification is crucial for ensuring the reliability and longevity of the resistor in high-current applications.
C. Simulation and Prototyping
Before moving to production, engineers often use simulation tools to model the performance of the resistor under various conditions. Prototyping allows for testing and validation of the design, ensuring that it meets the required specifications.
V. Manufacturing Process
A. Material Preparation
1. Sourcing and Quality Control
The first step in the manufacturing process is sourcing high-quality raw materials. Manufacturers must establish relationships with reliable suppliers and implement stringent quality control measures to ensure material consistency.
2. Material Processing
Once the materials are sourced, they undergo processing to prepare them for fabrication. This may include cutting, shaping, and treating the materials to achieve the desired properties.
B. Fabrication Techniques
1. Thin Film Deposition
Thin film resistors are produced using deposition techniques, such as sputtering or chemical vapor deposition. These methods allow for precise control over the thickness and composition of the resistive layer.
2. Thick Film Printing
Thick film resistors are created using screen printing techniques, where a paste of resistive material is applied to the substrate. After printing, the resistors are fired to cure the paste and form a solid resistive layer.
3. Wirewound Techniques
Wirewound resistors are fabricated by winding a metal wire around a core. This process requires careful handling to ensure uniformity and consistency in the winding.
C. Assembly
1. Mounting on Substrates
After fabrication, the resistors are mounted on substrates, which may involve adhesive bonding or mechanical fastening. This step is crucial for ensuring proper electrical connections and thermal management.
2. Soldering and Connections
Soldering is performed to create reliable electrical connections between the resistor and the circuit. This process must be executed with precision to avoid damaging the components.
VI. Testing and Quality Assurance
A. Electrical Testing
1. Resistance Measurement
Electrical testing begins with measuring the resistance of each resistor to ensure it meets the specified value. Automated testing equipment is often used for efficiency and accuracy.
2. Power Rating Tests
Power rating tests are conducted to verify that the resistors can handle the specified power levels without overheating or failing.
B. Environmental Testing
1. Temperature Cycling
Temperature cycling tests expose resistors to extreme temperature variations to assess their performance and reliability under real-world conditions.
2. Humidity and Moisture Resistance
Humidity tests evaluate the resistors' ability to withstand moisture, which is critical for ensuring long-term reliability in various environments.
C. Reliability Testing
1. Life Cycle Testing
Life cycle testing simulates the operational life of the resistors to identify potential failure modes and ensure they meet longevity expectations.
2. Stress Testing
Stress testing involves subjecting the resistors to extreme conditions, such as high currents or voltages, to evaluate their performance limits and durability.
VII. Packaging and Distribution
A. Packaging Materials
Once testing is complete, the resistors are packaged using materials that protect them from physical damage and environmental factors during transportation and storage.
B. Labeling and Documentation
Proper labeling and documentation are essential for traceability and compliance with industry standards. This information typically includes specifications, testing results, and safety warnings.
C. Distribution Channels
Current sensing resistors are distributed through various channels, including direct sales to manufacturers, electronic component distributors, and online marketplaces. Efficient distribution is crucial for meeting customer demand and ensuring timely delivery.
VIII. Conclusion
A. Summary of the Production Process
The production process of mainstream current sensing resistors is a complex and multifaceted endeavor that requires careful attention to detail at every stage. From raw material selection to final testing and packaging, each step plays a vital role in ensuring the quality and reliability of the final product.
B. Future Trends in Current Sensing Resistor Technology
As technology continues to evolve, the demand for more precise and efficient current sensing resistors is expected to grow. Innovations in materials, fabrication techniques, and design methodologies will likely lead to the development of even more advanced resistors that can meet the needs of emerging applications, such as electric vehicles and renewable energy systems.
C. Importance of Quality in Production
Quality assurance is paramount in the production of current sensing resistors. Manufacturers must adhere to strict standards and continuously improve their processes to ensure that their products meet the high expectations of the electronics industry. By prioritizing quality, manufacturers can enhance the performance and reliability of their resistors, ultimately contributing to the success of the electronic systems they support.
IX. References
A. Academic Journals
- Journal of Electronic Materials
- IEEE Transactions on Components, Packaging and Manufacturing Technology
B. Industry Standards
- IEC 60115: Fixed Resistors for Use in Electronic Equipment
- MIL-PRF-55182: Resistors, Fixed, Film, Thin and Thick
C. Manufacturer Guidelines
- Manufacturer datasheets and application notes
- Industry best practices for resistor design and testing
---
This blog post provides a comprehensive overview of the production process of mainstream current sensing resistors, highlighting the importance of each step in ensuring quality and reliability. By understanding this process, engineers and manufacturers can make informed decisions when selecting and producing these critical components.
The Production Process of Mainstream Current Sensing Resistors
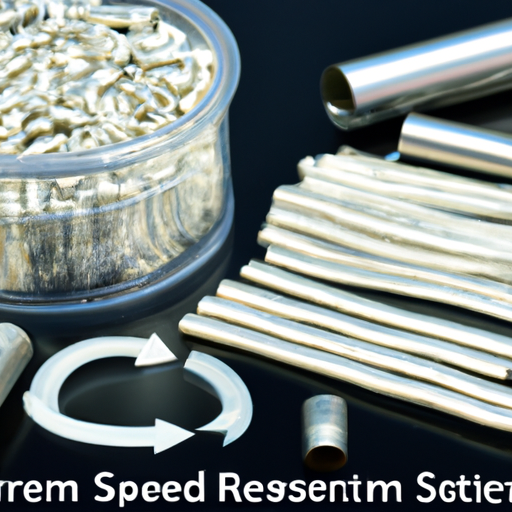
I. Introduction
A. Definition of Current Sensing Resistors
Current sensing resistors, often referred to as shunt resistors, are critical components in electronic circuits that measure the flow of electric current. By providing a known resistance, these resistors allow for the calculation of current based on the voltage drop across them, following Ohm's Law (V = IR). This functionality is essential in various applications, including power management, battery monitoring, and motor control.
B. Importance in Electronic Circuits
In modern electronics, the ability to accurately measure current is vital for system efficiency and safety. Current sensing resistors play a crucial role in protecting circuits from overcurrent conditions, enabling feedback mechanisms in power supplies, and ensuring optimal performance in battery-operated devices. Their reliability and precision directly impact the overall performance of electronic systems.
C. Overview of the Production Process
The production of current sensing resistors involves several stages, from raw material selection to final testing and packaging. Each step is critical to ensure that the resistors meet the required electrical and mechanical specifications. This blog post will delve into the various aspects of the production process, highlighting the importance of quality and innovation in this field.
II. Types of Current Sensing Resistors
A. Shunt Resistors
Shunt resistors are the most common type of current sensing resistors. They are typically low-resistance components placed in series with the load to measure current flow. Their design minimizes power loss while providing accurate current readings.
B. Wirewound Resistors
Wirewound resistors are constructed by winding a metal wire around a ceramic or fiberglass core. This design allows for high power ratings and excellent thermal stability, making them suitable for high-current applications.
C. Thin Film Resistors
Thin film resistors are made by depositing a thin layer of resistive material onto a substrate. They offer high precision and stability, making them ideal for applications requiring tight tolerances.
D. Thick Film Resistors
Thick film resistors are produced by printing a paste of resistive material onto a substrate and then firing it at high temperatures. They are cost-effective and widely used in various applications, though they may not offer the same precision as thin film resistors.
E. Comparison of Types
Each type of current sensing resistor has its advantages and disadvantages, depending on the application requirements. Shunt resistors are favored for their simplicity and low cost, while thin film resistors are preferred for high-precision applications. Understanding these differences is crucial for selecting the right resistor for a specific application.
III. Raw Materials
A. Conductive Materials
1. Metal Alloys
The choice of conductive materials is critical in the production of current sensing resistors. Metal alloys, such as nickel-chrome or copper-nickel, are commonly used due to their stable resistance characteristics and good thermal properties.
2. Carbon Composition
Carbon composition materials are also used, particularly in applications where high power ratings are required. They offer good thermal stability and are less susceptible to temperature variations.
B. Substrates
1. Ceramic
Ceramic substrates are often used for their excellent thermal conductivity and electrical insulation properties. They provide a stable base for resistive materials and help dissipate heat effectively.
2. Epoxy
Epoxy substrates are another option, particularly for thick film resistors. They are lightweight and can be molded into various shapes, making them versatile for different applications.
C. Coatings and Insulators
Coatings and insulators are applied to protect the resistors from environmental factors and to enhance their performance. These materials help prevent moisture ingress and improve the overall durability of the resistors.
IV. Design and Engineering
A. Electrical Specifications
1. Resistance Value
The resistance value is a critical parameter that determines the current sensing capability of the resistor. Engineers must carefully calculate the desired resistance based on the application requirements.
2. Tolerance
Tolerance indicates the allowable deviation from the specified resistance value. High-precision applications require resistors with tight tolerances to ensure accurate measurements.
3. Temperature Coefficient
The temperature coefficient measures how much the resistance changes with temperature. A low temperature coefficient is desirable for applications where temperature fluctuations are expected.
B. Mechanical Specifications
1. Size and Form Factor
The size and form factor of current sensing resistors are essential for integration into electronic circuits. Designers must consider the available space and the thermal management requirements when selecting resistor dimensions.
2. Power Rating
Power rating indicates the maximum power the resistor can handle without overheating. This specification is crucial for ensuring the reliability and longevity of the resistor in high-current applications.
C. Simulation and Prototyping
Before moving to production, engineers often use simulation tools to model the performance of the resistor under various conditions. Prototyping allows for testing and validation of the design, ensuring that it meets the required specifications.
V. Manufacturing Process
A. Material Preparation
1. Sourcing and Quality Control
The first step in the manufacturing process is sourcing high-quality raw materials. Manufacturers must establish relationships with reliable suppliers and implement stringent quality control measures to ensure material consistency.
2. Material Processing
Once the materials are sourced, they undergo processing to prepare them for fabrication. This may include cutting, shaping, and treating the materials to achieve the desired properties.
B. Fabrication Techniques
1. Thin Film Deposition
Thin film resistors are produced using deposition techniques, such as sputtering or chemical vapor deposition. These methods allow for precise control over the thickness and composition of the resistive layer.
2. Thick Film Printing
Thick film resistors are created using screen printing techniques, where a paste of resistive material is applied to the substrate. After printing, the resistors are fired to cure the paste and form a solid resistive layer.
3. Wirewound Techniques
Wirewound resistors are fabricated by winding a metal wire around a core. This process requires careful handling to ensure uniformity and consistency in the winding.
C. Assembly
1. Mounting on Substrates
After fabrication, the resistors are mounted on substrates, which may involve adhesive bonding or mechanical fastening. This step is crucial for ensuring proper electrical connections and thermal management.
2. Soldering and Connections
Soldering is performed to create reliable electrical connections between the resistor and the circuit. This process must be executed with precision to avoid damaging the components.
VI. Testing and Quality Assurance
A. Electrical Testing
1. Resistance Measurement
Electrical testing begins with measuring the resistance of each resistor to ensure it meets the specified value. Automated testing equipment is often used for efficiency and accuracy.
2. Power Rating Tests
Power rating tests are conducted to verify that the resistors can handle the specified power levels without overheating or failing.
B. Environmental Testing
1. Temperature Cycling
Temperature cycling tests expose resistors to extreme temperature variations to assess their performance and reliability under real-world conditions.
2. Humidity and Moisture Resistance
Humidity tests evaluate the resistors' ability to withstand moisture, which is critical for ensuring long-term reliability in various environments.
C. Reliability Testing
1. Life Cycle Testing
Life cycle testing simulates the operational life of the resistors to identify potential failure modes and ensure they meet longevity expectations.
2. Stress Testing
Stress testing involves subjecting the resistors to extreme conditions, such as high currents or voltages, to evaluate their performance limits and durability.
VII. Packaging and Distribution
A. Packaging Materials
Once testing is complete, the resistors are packaged using materials that protect them from physical damage and environmental factors during transportation and storage.
B. Labeling and Documentation
Proper labeling and documentation are essential for traceability and compliance with industry standards. This information typically includes specifications, testing results, and safety warnings.
C. Distribution Channels
Current sensing resistors are distributed through various channels, including direct sales to manufacturers, electronic component distributors, and online marketplaces. Efficient distribution is crucial for meeting customer demand and ensuring timely delivery.
VIII. Conclusion
A. Summary of the Production Process
The production process of mainstream current sensing resistors is a complex and multifaceted endeavor that requires careful attention to detail at every stage. From raw material selection to final testing and packaging, each step plays a vital role in ensuring the quality and reliability of the final product.
B. Future Trends in Current Sensing Resistor Technology
As technology continues to evolve, the demand for more precise and efficient current sensing resistors is expected to grow. Innovations in materials, fabrication techniques, and design methodologies will likely lead to the development of even more advanced resistors that can meet the needs of emerging applications, such as electric vehicles and renewable energy systems.
C. Importance of Quality in Production
Quality assurance is paramount in the production of current sensing resistors. Manufacturers must adhere to strict standards and continuously improve their processes to ensure that their products meet the high expectations of the electronics industry. By prioritizing quality, manufacturers can enhance the performance and reliability of their resistors, ultimately contributing to the success of the electronic systems they support.
IX. References
A. Academic Journals
- Journal of Electronic Materials
- IEEE Transactions on Components, Packaging and Manufacturing Technology
B. Industry Standards
- IEC 60115: Fixed Resistors for Use in Electronic Equipment
- MIL-PRF-55182: Resistors, Fixed, Film, Thin and Thick
C. Manufacturer Guidelines
- Manufacturer datasheets and application notes
- Industry best practices for resistor design and testing
---
This blog post provides a comprehensive overview of the production process of mainstream current sensing resistors, highlighting the importance of each step in ensuring quality and reliability. By understanding this process, engineers and manufacturers can make informed decisions when selecting and producing these critical components.