What is the Standard Production Process for Mainstream Resistors?
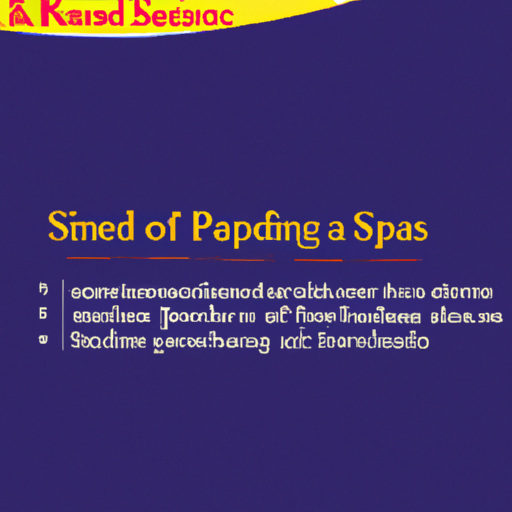
I. Introduction
Resistors are fundamental components in electronic circuits, serving the crucial role of controlling the flow of electric current. By providing resistance, they help to manage voltage levels, protect sensitive components, and ensure the proper functioning of devices. Given their importance, understanding the production process of mainstream resistors is essential for anyone involved in electronics, whether as a hobbyist, engineer, or manufacturer. This blog post will explore the various types of resistors, the raw materials used, the detailed production process, and future trends in resistor manufacturing.
II. Types of Resistors
Resistors come in various types, each designed for specific applications and performance characteristics.
A. Fixed Resistors
1. **Carbon Composition Resistors**: Made from a mixture of carbon and a binding material, these resistors are known for their high energy absorption and are often used in high-voltage applications.
2. **Metal Film Resistors**: These resistors are made by depositing a thin layer of metal onto a ceramic substrate. They offer high precision and stability, making them suitable for applications requiring accuracy.
3. **Carbon Film Resistors**: Similar to metal film resistors, but made from a carbon layer, these resistors provide good performance and are commonly used in consumer electronics.
4. **Wirewound Resistors**: Constructed by winding a metal wire around a ceramic or fiberglass core, wirewound resistors can handle high power levels and are often used in power applications.
B. Variable Resistors
1. **Potentiometers**: These resistors allow for adjustable resistance and are commonly used in volume controls and tuning circuits.
2. **Rheostats**: A type of variable resistor, rheostats are used to control current in a circuit and are often found in applications requiring high power.
C. Specialty Resistors
1. **Thermistors**: Temperature-sensitive resistors that change resistance with temperature variations, thermistors are widely used in temperature sensing and control applications.
2. **Photoresistors**: Also known as LDRs (Light Dependent Resistors), these resistors change resistance based on light exposure and are commonly used in light-sensing applications.
III. Raw Materials
The production of resistors relies on a variety of raw materials, each contributing to the resistor's performance and characteristics.
A. Conductive Materials
1. **Carbon**: Used primarily in carbon composition and carbon film resistors, carbon provides a stable and reliable resistance.
2. **Metal Oxides**: Commonly used in metal film resistors, metal oxides offer high stability and precision.
3. **Metal Wires**: Essential for wirewound resistors, metal wires (often made of nickel-chromium or copper) provide the necessary conductivity.
B. Insulating Materials
1. **Ceramic**: Used as a substrate for many resistors, ceramic materials provide excellent insulation and thermal stability.
2. **Epoxy**: Often used for coating and protecting resistors, epoxy provides durability and resistance to environmental factors.
3. **Plastic**: Used in packaging and some resistor types, plastic materials offer lightweight and cost-effective solutions.
IV. The Production Process
The production of resistors involves several key steps, from design to final testing.
A. Design and Engineering
1. **Specifications and Requirements**: The first step in the production process is defining the specifications for the resistor, including resistance value, tolerance, power rating, and environmental conditions.
2. **Prototyping**: Engineers create prototypes to test the design and ensure it meets the required specifications before moving to mass production.
B. Material Preparation
1. **Sourcing Raw Materials**: Manufacturers source high-quality raw materials from reliable suppliers to ensure the performance and reliability of the final product.
2. **Quality Control of Materials**: Incoming materials undergo rigorous quality control checks to ensure they meet the necessary standards.
C. Manufacturing Steps
1. **Mixing and Forming**:
- **Carbon Composition**: The carbon and binding materials are mixed and formed into a cylindrical shape.
- **Metal Film Deposition**: A thin layer of metal is deposited onto a ceramic substrate using techniques like sputtering or evaporation.
2. **Cutting and Shaping**:
- **Wirewound Resistor Winding**: Metal wire is wound around a core to create the desired resistance.
- **Film Cutting**: For film resistors, the deposited film is cut into the required shapes and sizes.
3. **Sintering and Curing**:
- **High-Temperature Processes**: Resistors are subjected to high temperatures to enhance their structural integrity and performance.
- **Chemical Curing**: Some materials, like epoxy, undergo chemical curing to achieve the desired properties.
4. **Coating and Finishing**:
- **Protective Coatings**: Resistors are coated with protective materials to enhance durability and resistance to environmental factors.
- **Marking and Labeling**: Each resistor is marked with its specifications, including resistance value and tolerance, for easy identification.
D. Testing and Quality Assurance
1. **Electrical Testing**: Each batch of resistors undergoes electrical testing to ensure they meet the specified resistance values and tolerances.
2. **Environmental Testing**: Resistors are tested under various environmental conditions (temperature, humidity, etc.) to ensure reliability in real-world applications.
3. **Compliance with Standards**: Manufacturers ensure that their products comply with industry standards and regulations, such as those set by the International Electrotechnical Commission (IEC).
V. Packaging and Distribution
Once the resistors have passed all quality checks, they are prepared for packaging and distribution.
A. Packaging Methods
Resistors are typically packaged in bulk or in individual units, depending on customer requirements. Packaging must protect the resistors from physical damage and environmental factors.
B. Inventory Management
Effective inventory management ensures that manufacturers can meet demand without overproducing, which can lead to waste.
C. Distribution Channels
Resistors are distributed through various channels, including direct sales to manufacturers, electronic component distributors, and online platforms.
VI. Environmental Considerations
As the electronics industry grows, so does the need for sustainable practices in resistor production.
A. Waste Management
Manufacturers implement waste management strategies to minimize waste generated during production, including recycling scrap materials.
B. Recycling of Materials
Efforts are made to recycle materials used in resistors, such as metals and plastics, to reduce environmental impact.
C. Compliance with Environmental Regulations
Manufacturers must comply with environmental regulations, such as the Restriction of Hazardous Substances (RoHS) directive, to ensure their products are safe for the environment.
VII. Future Trends in Resistor Production
The resistor manufacturing industry is evolving, driven by technological advancements and market demands.
A. Technological Advancements
Innovations in materials and manufacturing processes are leading to the development of more efficient and reliable resistors.
B. Market Demands and Innovations
As electronic devices become more complex, there is a growing demand for resistors with higher precision and stability, prompting manufacturers to innovate.
C. Sustainability Initiatives
The industry is increasingly focusing on sustainability, with initiatives aimed at reducing waste, improving energy efficiency, and using eco-friendly materials.
VIII. Conclusion
In summary, the production process for mainstream resistors is a complex and multi-faceted operation that involves careful design, material selection, and rigorous testing. The importance of quality in resistor manufacturing cannot be overstated, as it directly impacts the performance and reliability of electronic devices. As the industry continues to evolve, embracing technological advancements and sustainability initiatives will be crucial for meeting future demands. Understanding this production process not only enhances our appreciation for these essential components but also highlights the intricate world of electronics that powers our daily lives.
What is the Standard Production Process for Mainstream Resistors?
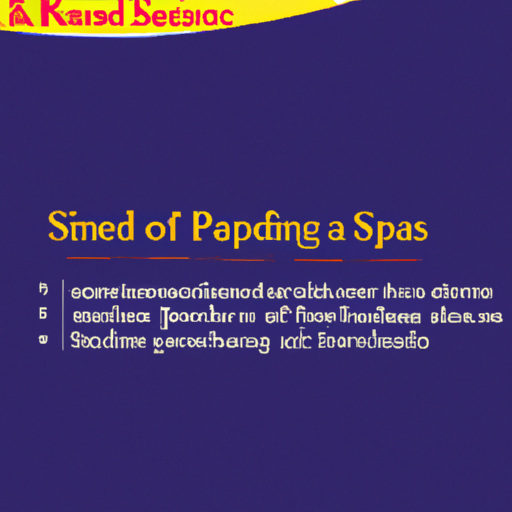
I. Introduction
Resistors are fundamental components in electronic circuits, serving the crucial role of controlling the flow of electric current. By providing resistance, they help to manage voltage levels, protect sensitive components, and ensure the proper functioning of devices. Given their importance, understanding the production process of mainstream resistors is essential for anyone involved in electronics, whether as a hobbyist, engineer, or manufacturer. This blog post will explore the various types of resistors, the raw materials used, the detailed production process, and future trends in resistor manufacturing.
II. Types of Resistors
Resistors come in various types, each designed for specific applications and performance characteristics.
A. Fixed Resistors
1. **Carbon Composition Resistors**: Made from a mixture of carbon and a binding material, these resistors are known for their high energy absorption and are often used in high-voltage applications.
2. **Metal Film Resistors**: These resistors are made by depositing a thin layer of metal onto a ceramic substrate. They offer high precision and stability, making them suitable for applications requiring accuracy.
3. **Carbon Film Resistors**: Similar to metal film resistors, but made from a carbon layer, these resistors provide good performance and are commonly used in consumer electronics.
4. **Wirewound Resistors**: Constructed by winding a metal wire around a ceramic or fiberglass core, wirewound resistors can handle high power levels and are often used in power applications.
B. Variable Resistors
1. **Potentiometers**: These resistors allow for adjustable resistance and are commonly used in volume controls and tuning circuits.
2. **Rheostats**: A type of variable resistor, rheostats are used to control current in a circuit and are often found in applications requiring high power.
C. Specialty Resistors
1. **Thermistors**: Temperature-sensitive resistors that change resistance with temperature variations, thermistors are widely used in temperature sensing and control applications.
2. **Photoresistors**: Also known as LDRs (Light Dependent Resistors), these resistors change resistance based on light exposure and are commonly used in light-sensing applications.
III. Raw Materials
The production of resistors relies on a variety of raw materials, each contributing to the resistor's performance and characteristics.
A. Conductive Materials
1. **Carbon**: Used primarily in carbon composition and carbon film resistors, carbon provides a stable and reliable resistance.
2. **Metal Oxides**: Commonly used in metal film resistors, metal oxides offer high stability and precision.
3. **Metal Wires**: Essential for wirewound resistors, metal wires (often made of nickel-chromium or copper) provide the necessary conductivity.
B. Insulating Materials
1. **Ceramic**: Used as a substrate for many resistors, ceramic materials provide excellent insulation and thermal stability.
2. **Epoxy**: Often used for coating and protecting resistors, epoxy provides durability and resistance to environmental factors.
3. **Plastic**: Used in packaging and some resistor types, plastic materials offer lightweight and cost-effective solutions.
IV. The Production Process
The production of resistors involves several key steps, from design to final testing.
A. Design and Engineering
1. **Specifications and Requirements**: The first step in the production process is defining the specifications for the resistor, including resistance value, tolerance, power rating, and environmental conditions.
2. **Prototyping**: Engineers create prototypes to test the design and ensure it meets the required specifications before moving to mass production.
B. Material Preparation
1. **Sourcing Raw Materials**: Manufacturers source high-quality raw materials from reliable suppliers to ensure the performance and reliability of the final product.
2. **Quality Control of Materials**: Incoming materials undergo rigorous quality control checks to ensure they meet the necessary standards.
C. Manufacturing Steps
1. **Mixing and Forming**:
- **Carbon Composition**: The carbon and binding materials are mixed and formed into a cylindrical shape.
- **Metal Film Deposition**: A thin layer of metal is deposited onto a ceramic substrate using techniques like sputtering or evaporation.
2. **Cutting and Shaping**:
- **Wirewound Resistor Winding**: Metal wire is wound around a core to create the desired resistance.
- **Film Cutting**: For film resistors, the deposited film is cut into the required shapes and sizes.
3. **Sintering and Curing**:
- **High-Temperature Processes**: Resistors are subjected to high temperatures to enhance their structural integrity and performance.
- **Chemical Curing**: Some materials, like epoxy, undergo chemical curing to achieve the desired properties.
4. **Coating and Finishing**:
- **Protective Coatings**: Resistors are coated with protective materials to enhance durability and resistance to environmental factors.
- **Marking and Labeling**: Each resistor is marked with its specifications, including resistance value and tolerance, for easy identification.
D. Testing and Quality Assurance
1. **Electrical Testing**: Each batch of resistors undergoes electrical testing to ensure they meet the specified resistance values and tolerances.
2. **Environmental Testing**: Resistors are tested under various environmental conditions (temperature, humidity, etc.) to ensure reliability in real-world applications.
3. **Compliance with Standards**: Manufacturers ensure that their products comply with industry standards and regulations, such as those set by the International Electrotechnical Commission (IEC).
V. Packaging and Distribution
Once the resistors have passed all quality checks, they are prepared for packaging and distribution.
A. Packaging Methods
Resistors are typically packaged in bulk or in individual units, depending on customer requirements. Packaging must protect the resistors from physical damage and environmental factors.
B. Inventory Management
Effective inventory management ensures that manufacturers can meet demand without overproducing, which can lead to waste.
C. Distribution Channels
Resistors are distributed through various channels, including direct sales to manufacturers, electronic component distributors, and online platforms.
VI. Environmental Considerations
As the electronics industry grows, so does the need for sustainable practices in resistor production.
A. Waste Management
Manufacturers implement waste management strategies to minimize waste generated during production, including recycling scrap materials.
B. Recycling of Materials
Efforts are made to recycle materials used in resistors, such as metals and plastics, to reduce environmental impact.
C. Compliance with Environmental Regulations
Manufacturers must comply with environmental regulations, such as the Restriction of Hazardous Substances (RoHS) directive, to ensure their products are safe for the environment.
VII. Future Trends in Resistor Production
The resistor manufacturing industry is evolving, driven by technological advancements and market demands.
A. Technological Advancements
Innovations in materials and manufacturing processes are leading to the development of more efficient and reliable resistors.
B. Market Demands and Innovations
As electronic devices become more complex, there is a growing demand for resistors with higher precision and stability, prompting manufacturers to innovate.
C. Sustainability Initiatives
The industry is increasingly focusing on sustainability, with initiatives aimed at reducing waste, improving energy efficiency, and using eco-friendly materials.
VIII. Conclusion
In summary, the production process for mainstream resistors is a complex and multi-faceted operation that involves careful design, material selection, and rigorous testing. The importance of quality in resistor manufacturing cannot be overstated, as it directly impacts the performance and reliability of electronic devices. As the industry continues to evolve, embracing technological advancements and sustainability initiatives will be crucial for meeting future demands. Understanding this production process not only enhances our appreciation for these essential components but also highlights the intricate world of electronics that powers our daily lives.