Common Production Processes for Resistors
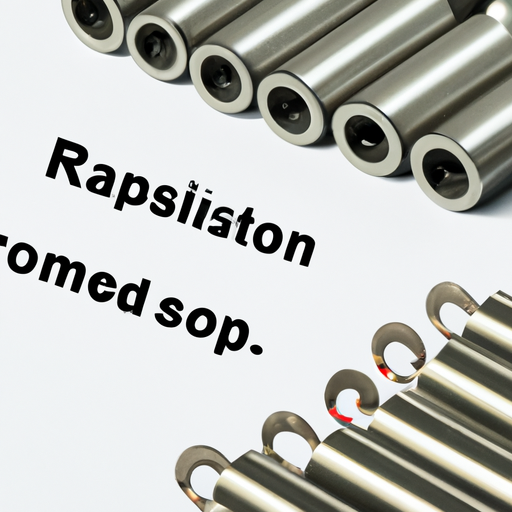
I. Introduction
Resistors are fundamental components in electronic circuits, serving the crucial role of controlling the flow of electric current. By providing resistance, they help to manage voltage levels, protect sensitive components, and ensure the proper functioning of electronic devices. The production of resistors involves a series of intricate processes that transform raw materials into reliable components used in everything from household appliances to advanced computing systems. This blog post will explore the common production processes for resistors, delving into the types of resistors, raw materials, manufacturing techniques, quality control measures, environmental considerations, and future trends in resistor production.
II. Types of Resistors
Resistors can be broadly categorized into fixed and variable types, each serving different functions in electronic circuits.
A. Fixed Resistors
1. **Carbon Composition Resistors**: These resistors are made from a mixture of carbon and a binding material. They are known for their high energy absorption and are often used in applications where high pulse loads are expected.
2. **Film Resistors**: This category includes:
- **Carbon Film Resistors**: Created by depositing a thin layer of carbon on a ceramic substrate, these resistors offer better stability and tolerance than carbon composition types.
- **Metal Film Resistors**: These resistors use a thin layer of metal, providing superior accuracy and stability.
- **Thin Film vs. Thick Film**: Thin film resistors are made with a more precise deposition process, resulting in lower noise and better performance, while thick film resistors are more cost-effective and widely used.
3. **Wirewound Resistors**: Constructed by winding a metal wire around a ceramic or fiberglass core, these resistors can handle high power levels and are often used in high-precision applications.
B. Variable Resistors
1. **Potentiometers**: These adjustable resistors allow users to change resistance levels manually, commonly found in volume controls and tuning circuits.
2. **Rheostats**: Similar to potentiometers but designed to handle higher currents, rheostats are used in applications requiring variable resistance.
C. Specialty Resistors
1. **Thermistors**: Temperature-sensitive resistors that change resistance with temperature variations, commonly used in temperature sensing and control applications.
2. **Photoresistors**: Also known as light-dependent resistors (LDRs), these components change resistance based on light exposure, making them ideal for light-sensing applications.
III. Raw Materials Used in Resistor Production
The production of resistors relies on a variety of raw materials, each contributing to the performance and characteristics of the final product.
A. Conductive Materials
1. **Carbon**: Used in carbon composition and carbon film resistors, carbon provides a stable and reliable resistance.
2. **Metal Oxides**: Commonly used in film resistors, metal oxides offer excellent thermal stability and resistance to environmental factors.
3. **Metal Alloys**: Utilized in wirewound resistors, metal alloys provide high conductivity and durability.
B. Insulating Materials
1. **Ceramics**: Often used as substrates for film resistors, ceramics provide excellent insulation and thermal stability.
2. **Epoxy Resins**: These materials are used for coating and encapsulating resistors, offering protection against moisture and mechanical stress.
3. **Plastics**: Used in various resistor types for insulation and housing, plastics are lightweight and cost-effective.
IV. Common Production Processes
The production of resistors involves several key processes, each tailored to the specific type of resistor being manufactured.
A. Carbon Composition Resistors
1. **Mixing of Raw Materials**: The production begins with the precise mixing of carbon powder and a binding agent to create a homogenous mixture.
2. **Molding and Shaping**: The mixture is then molded into the desired shape, typically cylindrical or rectangular.
3. **Curing and Finishing**: The molded resistors undergo a curing process to harden the material, followed by finishing steps to ensure uniformity and quality.
B. Film Resistors
1. **Substrate Preparation**: A ceramic substrate is prepared, cleaned, and coated with a conductive layer.
2. **Thin Film Deposition Techniques**: Techniques such as sputtering and chemical vapor deposition (CVD) are employed to deposit a thin layer of resistive material onto the substrate.
3. **Laser Trimming**: This process fine-tunes the resistance value by selectively removing material from the resistive layer.
4. **Coating and Encapsulation**: Finally, the resistors are coated with protective materials to enhance durability and performance.
C. Wirewound Resistors
1. **Wire Selection and Preparation**: High-quality metal wire is selected based on the desired resistance and power rating.
2. **Winding Process**: The wire is wound around a ceramic or fiberglass core, forming the resistive element.
3. **Insulation and Coating**: The wound resistor is insulated and coated to protect against environmental factors and ensure safety.
D. Variable Resistors
1. **Construction of the Resistive Element**: The resistive element is constructed using materials that allow for variable resistance.
2. **Assembly of Mechanical Components**: Mechanical components, such as sliders or knobs, are assembled to enable user adjustment.
3. **Testing and Calibration**: Each variable resistor undergoes testing and calibration to ensure accurate performance.
V. Quality Control in Resistor Production
Quality control is a critical aspect of resistor production, ensuring that each component meets industry standards and performs reliably.
A. Importance of Quality Control
Quality control helps to identify defects early in the production process, reducing waste and ensuring customer satisfaction.
B. Testing Methods
1. **Resistance Measurement**: Each resistor is tested for its resistance value to ensure it meets specifications.
2. **Temperature Coefficient Testing**: This test evaluates how resistance changes with temperature, ensuring stability in varying conditions.
3. **Endurance Testing**: Resistors undergo stress tests to assess their performance under extreme conditions, such as high temperatures and voltages.
C. Compliance with Standards
Manufacturers must comply with international standards set by organizations such as the International Electrotechnical Commission (IEC) and the American National Standards Institute (ANSI) to ensure product reliability and safety.
VI. Environmental Considerations
As the electronics industry evolves, so do the environmental considerations associated with resistor production.
A. Waste Management in Resistor Production
Efficient waste management practices are essential to minimize the environmental impact of resistor manufacturing. This includes recycling materials and reducing hazardous waste.
B. Use of Eco-Friendly Materials
The industry is increasingly adopting eco-friendly materials and processes to reduce the carbon footprint of resistor production.
C. Recycling of Resistors
Recycling programs for electronic components, including resistors, are being developed to recover valuable materials and reduce landfill waste.
VII. Future Trends in Resistor Production
The future of resistor production is shaped by advancements in technology and materials science.
A. Advances in Materials Science
Research into new materials, such as nanomaterials and advanced composites, is paving the way for resistors with improved performance and reliability.
B. Automation and Smart Manufacturing
The integration of automation and smart manufacturing techniques is enhancing production efficiency, reducing costs, and improving quality control.
C. Miniaturization and Integration with Other Components
As electronic devices become smaller and more complex, the demand for miniaturized resistors that can be integrated with other components is on the rise.
VIII. Conclusion
In summary, resistors play a vital role in modern electronics, and their production involves a complex interplay of materials, processes, and quality control measures. Understanding the common production processes for resistors not only highlights the intricacies of manufacturing but also underscores the importance of these components in ensuring the functionality and reliability of electronic devices. As the industry continues to evolve, innovations in materials and manufacturing techniques will shape the future of resistor production, paving the way for more efficient, reliable, and environmentally friendly components. The ongoing advancements in this field will undoubtedly enhance the performance of electronic devices, making them more efficient and sustainable for future generations.
Common Production Processes for Resistors
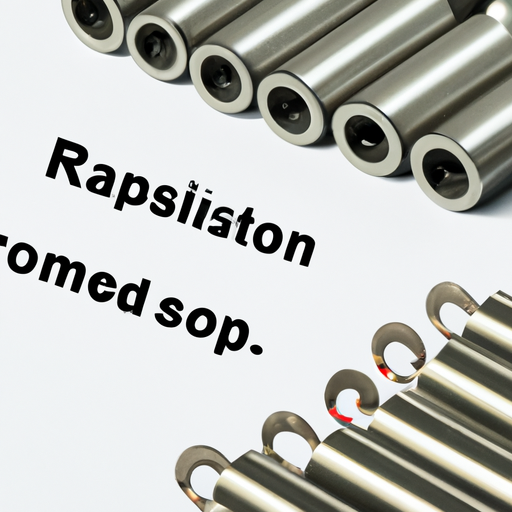
I. Introduction
Resistors are fundamental components in electronic circuits, serving the crucial role of controlling the flow of electric current. By providing resistance, they help to manage voltage levels, protect sensitive components, and ensure the proper functioning of electronic devices. The production of resistors involves a series of intricate processes that transform raw materials into reliable components used in everything from household appliances to advanced computing systems. This blog post will explore the common production processes for resistors, delving into the types of resistors, raw materials, manufacturing techniques, quality control measures, environmental considerations, and future trends in resistor production.
II. Types of Resistors
Resistors can be broadly categorized into fixed and variable types, each serving different functions in electronic circuits.
A. Fixed Resistors
1. **Carbon Composition Resistors**: These resistors are made from a mixture of carbon and a binding material. They are known for their high energy absorption and are often used in applications where high pulse loads are expected.
2. **Film Resistors**: This category includes:
- **Carbon Film Resistors**: Created by depositing a thin layer of carbon on a ceramic substrate, these resistors offer better stability and tolerance than carbon composition types.
- **Metal Film Resistors**: These resistors use a thin layer of metal, providing superior accuracy and stability.
- **Thin Film vs. Thick Film**: Thin film resistors are made with a more precise deposition process, resulting in lower noise and better performance, while thick film resistors are more cost-effective and widely used.
3. **Wirewound Resistors**: Constructed by winding a metal wire around a ceramic or fiberglass core, these resistors can handle high power levels and are often used in high-precision applications.
B. Variable Resistors
1. **Potentiometers**: These adjustable resistors allow users to change resistance levels manually, commonly found in volume controls and tuning circuits.
2. **Rheostats**: Similar to potentiometers but designed to handle higher currents, rheostats are used in applications requiring variable resistance.
C. Specialty Resistors
1. **Thermistors**: Temperature-sensitive resistors that change resistance with temperature variations, commonly used in temperature sensing and control applications.
2. **Photoresistors**: Also known as light-dependent resistors (LDRs), these components change resistance based on light exposure, making them ideal for light-sensing applications.
III. Raw Materials Used in Resistor Production
The production of resistors relies on a variety of raw materials, each contributing to the performance and characteristics of the final product.
A. Conductive Materials
1. **Carbon**: Used in carbon composition and carbon film resistors, carbon provides a stable and reliable resistance.
2. **Metal Oxides**: Commonly used in film resistors, metal oxides offer excellent thermal stability and resistance to environmental factors.
3. **Metal Alloys**: Utilized in wirewound resistors, metal alloys provide high conductivity and durability.
B. Insulating Materials
1. **Ceramics**: Often used as substrates for film resistors, ceramics provide excellent insulation and thermal stability.
2. **Epoxy Resins**: These materials are used for coating and encapsulating resistors, offering protection against moisture and mechanical stress.
3. **Plastics**: Used in various resistor types for insulation and housing, plastics are lightweight and cost-effective.
IV. Common Production Processes
The production of resistors involves several key processes, each tailored to the specific type of resistor being manufactured.
A. Carbon Composition Resistors
1. **Mixing of Raw Materials**: The production begins with the precise mixing of carbon powder and a binding agent to create a homogenous mixture.
2. **Molding and Shaping**: The mixture is then molded into the desired shape, typically cylindrical or rectangular.
3. **Curing and Finishing**: The molded resistors undergo a curing process to harden the material, followed by finishing steps to ensure uniformity and quality.
B. Film Resistors
1. **Substrate Preparation**: A ceramic substrate is prepared, cleaned, and coated with a conductive layer.
2. **Thin Film Deposition Techniques**: Techniques such as sputtering and chemical vapor deposition (CVD) are employed to deposit a thin layer of resistive material onto the substrate.
3. **Laser Trimming**: This process fine-tunes the resistance value by selectively removing material from the resistive layer.
4. **Coating and Encapsulation**: Finally, the resistors are coated with protective materials to enhance durability and performance.
C. Wirewound Resistors
1. **Wire Selection and Preparation**: High-quality metal wire is selected based on the desired resistance and power rating.
2. **Winding Process**: The wire is wound around a ceramic or fiberglass core, forming the resistive element.
3. **Insulation and Coating**: The wound resistor is insulated and coated to protect against environmental factors and ensure safety.
D. Variable Resistors
1. **Construction of the Resistive Element**: The resistive element is constructed using materials that allow for variable resistance.
2. **Assembly of Mechanical Components**: Mechanical components, such as sliders or knobs, are assembled to enable user adjustment.
3. **Testing and Calibration**: Each variable resistor undergoes testing and calibration to ensure accurate performance.
V. Quality Control in Resistor Production
Quality control is a critical aspect of resistor production, ensuring that each component meets industry standards and performs reliably.
A. Importance of Quality Control
Quality control helps to identify defects early in the production process, reducing waste and ensuring customer satisfaction.
B. Testing Methods
1. **Resistance Measurement**: Each resistor is tested for its resistance value to ensure it meets specifications.
2. **Temperature Coefficient Testing**: This test evaluates how resistance changes with temperature, ensuring stability in varying conditions.
3. **Endurance Testing**: Resistors undergo stress tests to assess their performance under extreme conditions, such as high temperatures and voltages.
C. Compliance with Standards
Manufacturers must comply with international standards set by organizations such as the International Electrotechnical Commission (IEC) and the American National Standards Institute (ANSI) to ensure product reliability and safety.
VI. Environmental Considerations
As the electronics industry evolves, so do the environmental considerations associated with resistor production.
A. Waste Management in Resistor Production
Efficient waste management practices are essential to minimize the environmental impact of resistor manufacturing. This includes recycling materials and reducing hazardous waste.
B. Use of Eco-Friendly Materials
The industry is increasingly adopting eco-friendly materials and processes to reduce the carbon footprint of resistor production.
C. Recycling of Resistors
Recycling programs for electronic components, including resistors, are being developed to recover valuable materials and reduce landfill waste.
VII. Future Trends in Resistor Production
The future of resistor production is shaped by advancements in technology and materials science.
A. Advances in Materials Science
Research into new materials, such as nanomaterials and advanced composites, is paving the way for resistors with improved performance and reliability.
B. Automation and Smart Manufacturing
The integration of automation and smart manufacturing techniques is enhancing production efficiency, reducing costs, and improving quality control.
C. Miniaturization and Integration with Other Components
As electronic devices become smaller and more complex, the demand for miniaturized resistors that can be integrated with other components is on the rise.
VIII. Conclusion
In summary, resistors play a vital role in modern electronics, and their production involves a complex interplay of materials, processes, and quality control measures. Understanding the common production processes for resistors not only highlights the intricacies of manufacturing but also underscores the importance of these components in ensuring the functionality and reliability of electronic devices. As the industry continues to evolve, innovations in materials and manufacturing techniques will shape the future of resistor production, paving the way for more efficient, reliable, and environmentally friendly components. The ongoing advancements in this field will undoubtedly enhance the performance of electronic devices, making them more efficient and sustainable for future generations.