What is the Mainstream Resistor Wiring Production Process?
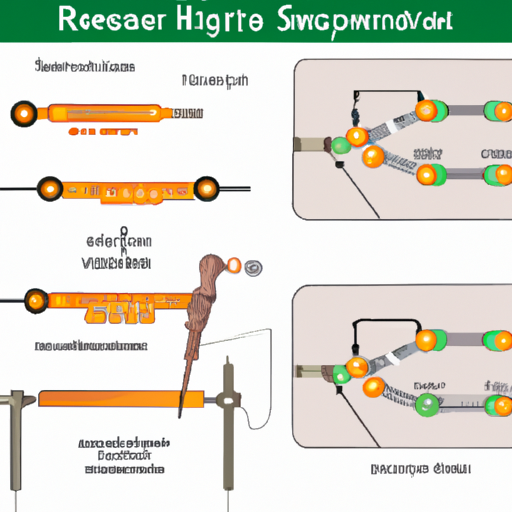
I. Introduction
Resistors are fundamental components in electronic circuits, serving the crucial role of controlling current flow and voltage levels. They are essential for the proper functioning of various devices, from simple household appliances to complex industrial machinery. The resistor manufacturing industry has evolved significantly over the years, driven by advancements in technology and increasing demand for electronic devices. This article aims to explore the mainstream resistor wiring production process, shedding light on the various stages involved in creating these vital components.
II. Types of Resistors
Resistors come in various types, each designed for specific applications. Understanding these types is essential for grasping the production process.
A. Fixed Resistors
1. **Carbon Composition Resistors**: Made from a mixture of carbon and a binding material, these resistors are known for their high tolerance and ability to withstand high temperatures. They are often used in applications where stability is crucial.
2. **Metal Film Resistors**: These resistors are constructed by depositing a thin layer of metal onto a ceramic substrate. They offer high precision and low noise, making them ideal for sensitive electronic circuits.
3. **Wirewound Resistors**: As the name suggests, these resistors are made by winding a metal wire around a ceramic or fiberglass core. They are capable of handling high power levels and are commonly used in power applications.
B. Variable Resistors
1. **Potentiometers**: These adjustable resistors allow users to change resistance levels manually. They are widely used in volume controls and other applications requiring variable resistance.
2. **Rheostats**: Similar to potentiometers, rheostats are used to control current flow in a circuit. They are typically used in applications where high power is involved.
C. Specialty Resistors
1. **Thermistors**: These temperature-sensitive resistors change resistance with temperature variations. They are commonly used in temperature sensing and control applications.
2. **Photoresistors**: Also known as light-dependent resistors (LDRs), these components change resistance based on light exposure. They are often used in light-sensing applications, such as automatic lighting systems.
III. Raw Materials Used in Resistor Production
The production of resistors involves various raw materials, each contributing to the final product's performance and reliability.
A. Conductive Materials
1. **Carbon**: Used primarily in carbon composition resistors, carbon provides a stable and reliable resistive element.
2. **Metal Alloys**: Alloys such as nickel-chromium are commonly used in metal film and wirewound resistors due to their excellent conductivity and stability.
B. Insulating Materials
1. **Ceramic**: This material is often used as a substrate for resistors, providing excellent thermal stability and electrical insulation.
2. **Epoxy Resins**: These resins are used for coating and encapsulating resistors, offering protection against environmental factors.
C. Other Components
1. **Lead Wires**: These are essential for connecting resistors to circuits, typically made from copper or other conductive materials.
2. **Protective Coatings**: Coatings are applied to resistors to enhance durability and resistance to environmental factors.
IV. The Resistor Manufacturing Process
The manufacturing process of resistors involves several key stages, each critical to ensuring the quality and performance of the final product.
A. Design and Engineering
The process begins with design and engineering, where specifications and requirements are established. Engineers create prototypes and conduct testing to ensure the resistors meet the desired performance criteria.
B. Material Preparation
Once the design is finalized, the next step is material preparation. This involves sourcing raw materials and conducting quality control checks to ensure they meet industry standards. Pre-processing of materials, such as grinding and mixing, is also performed to prepare them for fabrication.
C. Component Fabrication
1. **Carbon Composition and Metal Film Deposition**: For carbon composition resistors, a mixture of carbon and binding agents is formed into a cylindrical shape. In contrast, metal film resistors undergo a deposition process where a thin layer of metal is applied to a ceramic substrate.
2. **Wire Winding for Wirewound Resistors**: In this step, a metal wire is wound around a core to create the resistive element. The winding process must be precise to ensure consistent resistance values.
D. Assembly
The assembly stage involves combining the resistive and insulating materials. Lead wires are soldered onto the resistive element, ensuring a secure connection for circuit integration.
E. Curing and Finishing
After assembly, curing processes are applied to adhesives and coatings to enhance durability. Final finishing touches, such as trimming and painting, are performed to ensure the resistors meet aesthetic and functional standards.
V. Quality Control and Testing
Quality assurance is paramount in resistor production. Manufacturers implement rigorous testing methods to ensure each resistor meets performance standards.
A. Importance of Quality Assurance
Quality assurance helps prevent defects and ensures that resistors perform reliably in their intended applications. This is particularly important in industries where precision is critical.
B. Testing Methods
1. **Electrical Testing**: This involves measuring resistance values to ensure they align with specifications. Automated testing equipment is often used for efficiency.
2. **Environmental Testing**: Resistors are subjected to various environmental conditions, such as temperature and humidity, to assess their performance under different scenarios.
C. Certification and Compliance
Manufacturers must comply with industry standards and obtain certifications to demonstrate the quality and reliability of their products. This includes adherence to international standards such as ISO and RoHS.
VI. Packaging and Distribution
Once the resistors pass quality control, they are packaged and prepared for distribution.
A. Packaging Methods
Resistors are typically packaged in bulk or in individual units, depending on customer requirements. Packaging must protect the components from damage during transport and storage.
B. Logistics and Distribution Channels
Manufacturers utilize various logistics and distribution channels to deliver resistors to customers worldwide. This includes partnerships with distributors and direct sales to electronic manufacturers.
C. Market Trends and Demand
The demand for resistors continues to grow, driven by advancements in technology and the increasing prevalence of electronic devices. Manufacturers must stay attuned to market trends to remain competitive.
VII. Innovations and Future Trends in Resistor Manufacturing
The resistor manufacturing industry is witnessing several innovations and trends that are shaping its future.
A. Advances in Materials Science
Research into new materials is leading to the development of resistors with improved performance characteristics, such as higher precision and better thermal stability.
B. Automation and Industry 4.0
The integration of automation and Industry 4.0 technologies is streamlining the manufacturing process, enhancing efficiency, and reducing production costs.
C. Environmental Considerations and Sustainability
As environmental concerns grow, manufacturers are exploring sustainable practices, such as using eco-friendly materials and reducing waste in the production process.
VIII. Conclusion
In summary, the resistor wiring production process is a complex and multifaceted operation that involves various stages, from design and material preparation to assembly and quality control. Resistors play a vital role in modern electronics, and their importance will only continue to grow as technology advances. The future of the resistor manufacturing industry looks promising, with innovations in materials science, automation, and sustainability paving the way for more efficient and reliable products.
IX. References
1. Academic journals and articles on resistor technology and manufacturing processes.
2. Industry reports and white papers detailing market trends and innovations.
3. Manufacturer websites and technical documentation providing insights into specific resistor types and production methods.
This comprehensive overview of the mainstream resistor wiring production process highlights the intricacies involved in creating these essential components, emphasizing their significance in the ever-evolving world of electronics.
What is the Mainstream Resistor Wiring Production Process?
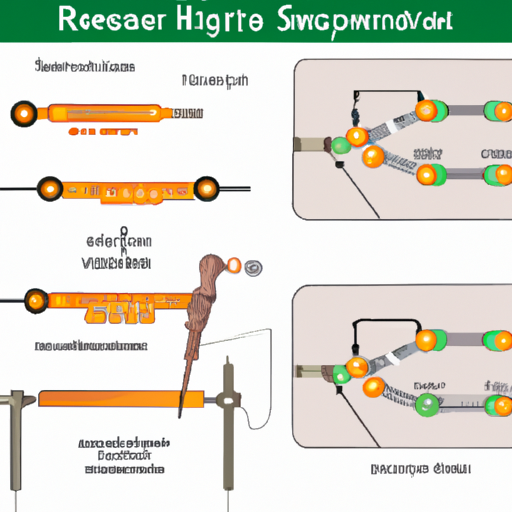
I. Introduction
Resistors are fundamental components in electronic circuits, serving the crucial role of controlling current flow and voltage levels. They are essential for the proper functioning of various devices, from simple household appliances to complex industrial machinery. The resistor manufacturing industry has evolved significantly over the years, driven by advancements in technology and increasing demand for electronic devices. This article aims to explore the mainstream resistor wiring production process, shedding light on the various stages involved in creating these vital components.
II. Types of Resistors
Resistors come in various types, each designed for specific applications. Understanding these types is essential for grasping the production process.
A. Fixed Resistors
1. **Carbon Composition Resistors**: Made from a mixture of carbon and a binding material, these resistors are known for their high tolerance and ability to withstand high temperatures. They are often used in applications where stability is crucial.
2. **Metal Film Resistors**: These resistors are constructed by depositing a thin layer of metal onto a ceramic substrate. They offer high precision and low noise, making them ideal for sensitive electronic circuits.
3. **Wirewound Resistors**: As the name suggests, these resistors are made by winding a metal wire around a ceramic or fiberglass core. They are capable of handling high power levels and are commonly used in power applications.
B. Variable Resistors
1. **Potentiometers**: These adjustable resistors allow users to change resistance levels manually. They are widely used in volume controls and other applications requiring variable resistance.
2. **Rheostats**: Similar to potentiometers, rheostats are used to control current flow in a circuit. They are typically used in applications where high power is involved.
C. Specialty Resistors
1. **Thermistors**: These temperature-sensitive resistors change resistance with temperature variations. They are commonly used in temperature sensing and control applications.
2. **Photoresistors**: Also known as light-dependent resistors (LDRs), these components change resistance based on light exposure. They are often used in light-sensing applications, such as automatic lighting systems.
III. Raw Materials Used in Resistor Production
The production of resistors involves various raw materials, each contributing to the final product's performance and reliability.
A. Conductive Materials
1. **Carbon**: Used primarily in carbon composition resistors, carbon provides a stable and reliable resistive element.
2. **Metal Alloys**: Alloys such as nickel-chromium are commonly used in metal film and wirewound resistors due to their excellent conductivity and stability.
B. Insulating Materials
1. **Ceramic**: This material is often used as a substrate for resistors, providing excellent thermal stability and electrical insulation.
2. **Epoxy Resins**: These resins are used for coating and encapsulating resistors, offering protection against environmental factors.
C. Other Components
1. **Lead Wires**: These are essential for connecting resistors to circuits, typically made from copper or other conductive materials.
2. **Protective Coatings**: Coatings are applied to resistors to enhance durability and resistance to environmental factors.
IV. The Resistor Manufacturing Process
The manufacturing process of resistors involves several key stages, each critical to ensuring the quality and performance of the final product.
A. Design and Engineering
The process begins with design and engineering, where specifications and requirements are established. Engineers create prototypes and conduct testing to ensure the resistors meet the desired performance criteria.
B. Material Preparation
Once the design is finalized, the next step is material preparation. This involves sourcing raw materials and conducting quality control checks to ensure they meet industry standards. Pre-processing of materials, such as grinding and mixing, is also performed to prepare them for fabrication.
C. Component Fabrication
1. **Carbon Composition and Metal Film Deposition**: For carbon composition resistors, a mixture of carbon and binding agents is formed into a cylindrical shape. In contrast, metal film resistors undergo a deposition process where a thin layer of metal is applied to a ceramic substrate.
2. **Wire Winding for Wirewound Resistors**: In this step, a metal wire is wound around a core to create the resistive element. The winding process must be precise to ensure consistent resistance values.
D. Assembly
The assembly stage involves combining the resistive and insulating materials. Lead wires are soldered onto the resistive element, ensuring a secure connection for circuit integration.
E. Curing and Finishing
After assembly, curing processes are applied to adhesives and coatings to enhance durability. Final finishing touches, such as trimming and painting, are performed to ensure the resistors meet aesthetic and functional standards.
V. Quality Control and Testing
Quality assurance is paramount in resistor production. Manufacturers implement rigorous testing methods to ensure each resistor meets performance standards.
A. Importance of Quality Assurance
Quality assurance helps prevent defects and ensures that resistors perform reliably in their intended applications. This is particularly important in industries where precision is critical.
B. Testing Methods
1. **Electrical Testing**: This involves measuring resistance values to ensure they align with specifications. Automated testing equipment is often used for efficiency.
2. **Environmental Testing**: Resistors are subjected to various environmental conditions, such as temperature and humidity, to assess their performance under different scenarios.
C. Certification and Compliance
Manufacturers must comply with industry standards and obtain certifications to demonstrate the quality and reliability of their products. This includes adherence to international standards such as ISO and RoHS.
VI. Packaging and Distribution
Once the resistors pass quality control, they are packaged and prepared for distribution.
A. Packaging Methods
Resistors are typically packaged in bulk or in individual units, depending on customer requirements. Packaging must protect the components from damage during transport and storage.
B. Logistics and Distribution Channels
Manufacturers utilize various logistics and distribution channels to deliver resistors to customers worldwide. This includes partnerships with distributors and direct sales to electronic manufacturers.
C. Market Trends and Demand
The demand for resistors continues to grow, driven by advancements in technology and the increasing prevalence of electronic devices. Manufacturers must stay attuned to market trends to remain competitive.
VII. Innovations and Future Trends in Resistor Manufacturing
The resistor manufacturing industry is witnessing several innovations and trends that are shaping its future.
A. Advances in Materials Science
Research into new materials is leading to the development of resistors with improved performance characteristics, such as higher precision and better thermal stability.
B. Automation and Industry 4.0
The integration of automation and Industry 4.0 technologies is streamlining the manufacturing process, enhancing efficiency, and reducing production costs.
C. Environmental Considerations and Sustainability
As environmental concerns grow, manufacturers are exploring sustainable practices, such as using eco-friendly materials and reducing waste in the production process.
VIII. Conclusion
In summary, the resistor wiring production process is a complex and multifaceted operation that involves various stages, from design and material preparation to assembly and quality control. Resistors play a vital role in modern electronics, and their importance will only continue to grow as technology advances. The future of the resistor manufacturing industry looks promising, with innovations in materials science, automation, and sustainability paving the way for more efficient and reliable products.
IX. References
1. Academic journals and articles on resistor technology and manufacturing processes.
2. Industry reports and white papers detailing market trends and innovations.
3. Manufacturer websites and technical documentation providing insights into specific resistor types and production methods.
This comprehensive overview of the mainstream resistor wiring production process highlights the intricacies involved in creating these essential components, emphasizing their significance in the ever-evolving world of electronics.