What are the Product Standards of Resistor Factories?
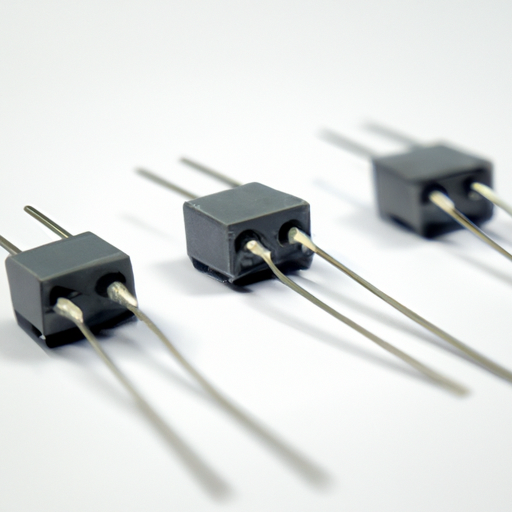
I. Introduction
Resistors are fundamental components in electronic circuits, serving the critical function of controlling current flow and voltage levels. Their importance cannot be overstated, as they are integral to the operation of virtually all electronic devices, from simple household appliances to complex computing systems. Given their pivotal role, the manufacturing of resistors is governed by stringent product standards that ensure quality, safety, and performance. This article aims to explore the various product standards that govern resistor factories, shedding light on their significance and the organizations that establish them.
II. Understanding Resistor Standards
Product standards in the context of resistors refer to the established criteria and specifications that manufacturers must adhere to during the production process. These standards are crucial for ensuring that resistors perform reliably and safely in their intended applications. They encompass various aspects, including electrical performance, safety, and environmental considerations.
International and national standards organizations play a vital role in developing and maintaining these standards. Their work ensures that resistors produced across different regions meet consistent quality benchmarks, facilitating global trade and enhancing consumer safety.
III. Key Standards Governing Resistor Manufacturing
A. International Electrotechnical Commission (IEC)
The International Electrotechnical Commission (IEC) is a leading organization that develops international standards for electrical and electronic technologies. One of the key standards relevant to resistors is IEC 60115, which outlines the general requirements for fixed resistors. This standard covers aspects such as resistance values, tolerances, temperature coefficients, and power ratings, ensuring that resistors meet specific performance criteria.
B. American National Standards Institute (ANSI)
In the United States, the American National Standards Institute (ANSI) plays a crucial role in setting standards for various industries, including electronics. ANSI standards applicable to resistor manufacturing include specifications for performance, safety, and testing methods. These standards help ensure that resistors produced in the U.S. meet the necessary quality and safety requirements.
C. Institute of Electrical and Electronics Engineers (IEEE)
The IEEE is another significant organization that contributes to the establishment of standards related to resistors. IEEE standards are particularly important in the context of electronic design, as they provide guidelines for the integration of resistors into complex circuits. These standards help engineers ensure that their designs are reliable and compliant with industry expectations.
D. Other Relevant Standards Organizations
Several other organizations contribute to the development of resistor standards, including:
International Organization for Standardization (ISO): ISO standards focus on quality management systems and environmental management, which can impact resistor manufacturing processes.
Underwriters Laboratories (UL): UL standards emphasize safety and performance, particularly in electrical components, including resistors.
European Committee for Electrotechnical Standardization (CENELEC): CENELEC develops standards for electrical and electronic products in Europe, ensuring compliance with regional regulations.
IV. Types of Resistor Standards
A. Performance Standards
Performance standards are critical for ensuring that resistors function as intended. Key aspects include:
1. **Tolerance Levels**: Tolerance indicates the permissible deviation from the nominal resistance value. Common tolerance levels for resistors range from ±1% to ±5%, with precision resistors offering tighter tolerances.
2. **Temperature Coefficient of Resistance (TCR)**: TCR measures how much a resistor's resistance changes with temperature. A lower TCR indicates better performance in varying temperature conditions.
3. **Power Rating and Derating**: The power rating specifies the maximum power a resistor can dissipate without failure. Derating involves operating the resistor below its maximum rating to enhance reliability and longevity.
B. Safety Standards
Safety standards are essential to prevent hazards associated with electrical components. Key safety considerations include:
1. **Electrical Safety Requirements**: Resistors must meet specific electrical safety criteria to prevent short circuits, overheating, and other electrical failures.
2. **Fire Safety and Flammability Testing**: Resistors are subjected to flammability tests to ensure they do not pose a fire risk under normal operating conditions.
C. Environmental Standards
Environmental standards address the ecological impact of resistor manufacturing and disposal. Important considerations include:
1. **RoHS Compliance**: The Restriction of Hazardous Substances (RoHS) directive limits the use of certain hazardous materials in electronic products, including resistors.
2. **REACH Compliance**: The Registration, Evaluation, Authorisation, and Restriction of Chemicals (REACH) regulation ensures that chemicals used in manufacturing are safe for human health and the environment.
3. **End-of-Life Disposal and Recycling Standards**: These standards promote responsible disposal and recycling of electronic components, reducing environmental impact.
V. Testing and Quality Assurance in Resistor Factories
A. Importance of Testing
Testing is a critical component of the manufacturing process, ensuring that resistors comply with established standards. Rigorous testing helps identify defects and ensures that products meet performance and safety requirements.
B. Common Testing Methods
1. **Electrical Testing**: This includes resistance measurement to verify that the resistor meets its specified value and tolerance.
2. **Environmental Testing**: Resistors undergo temperature cycling tests to assess their performance under varying thermal conditions.
3. **Mechanical Testing**: Vibration and shock tests evaluate the physical robustness of resistors, ensuring they can withstand real-world conditions.
C. Quality Assurance Processes
Quality assurance in resistor manufacturing involves several key processes:
1. **Incoming Material Inspection**: Raw materials are inspected to ensure they meet quality standards before production begins.
2. **In-Process Quality Control**: Continuous monitoring during the manufacturing process helps identify and rectify issues in real-time.
3. **Final Product Inspection and Testing**: Finished resistors undergo comprehensive testing to confirm compliance with all relevant standards before they are shipped to customers.
VI. Challenges in Meeting Product Standards
A. Technological Advancements
Rapid technological advancements can outpace existing standards, creating challenges for manufacturers. As new materials and designs emerge, standards must evolve to address these innovations.
B. Variability in Raw Materials
The quality and consistency of raw materials can significantly impact compliance with standards. Variability in material properties can lead to inconsistencies in resistor performance.
C. Globalization
As manufacturing becomes increasingly globalized, harmonizing standards across different regions is essential. Discrepancies in standards can create challenges for manufacturers operating in multiple markets.
D. Cost Implications
Adhering to stringent standards often involves additional costs related to testing, quality assurance, and compliance. Manufacturers must balance these costs with the need to produce high-quality products.
VII. Future Trends in Resistor Standards
A. Emerging Technologies
The rise of new technologies, such as IoT and AI, is influencing resistor design and standards. As electronic devices become more complex, standards will need to adapt to ensure compatibility and performance.
B. Sustainability
Sustainability is becoming a key focus in the electronics industry. Future standards are likely to emphasize environmentally friendly materials and manufacturing processes, promoting a circular economy.
C. Regulatory Changes
Anticipated changes in regulatory frameworks may lead to stricter compliance requirements. Manufacturers must stay informed about evolving regulations to ensure ongoing compliance.
VIII. Conclusion
In conclusion, product standards play a vital role in the manufacturing of resistors, ensuring quality, safety, and performance. Adherence to these standards is essential for manufacturers to meet customer expectations and regulatory requirements. As the electronics industry continues to evolve, the importance of robust product standards will only increase, shaping the future of resistor manufacturing and electronic design.
IX. References
- IEC 60115: Fixed Resistors for Use in Electronic Equipment
- ANSI Standards for Resistors
- IEEE Standards for Electronic Design
- RoHS Directive
- REACH Regulation
- ISO 9001: Quality Management Systems
- UL Standards for Electrical Components
This comprehensive overview of product standards in resistor factories highlights the critical role these standards play in ensuring the reliability and safety of electronic components. As technology advances and environmental considerations become more prominent, the landscape of resistor standards will continue to evolve, necessitating ongoing attention from manufacturers and engineers alike.
What are the Product Standards of Resistor Factories?
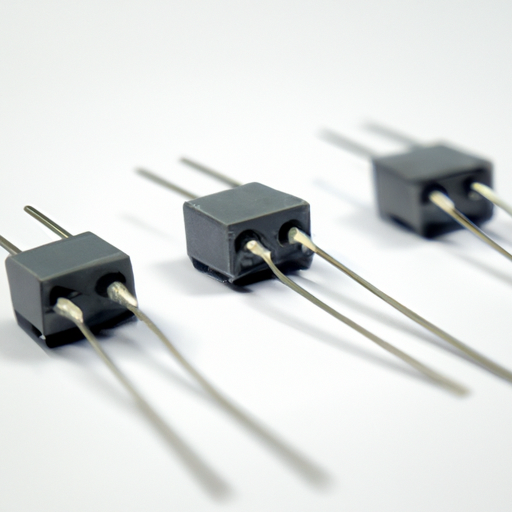
I. Introduction
Resistors are fundamental components in electronic circuits, serving the critical function of controlling current flow and voltage levels. Their importance cannot be overstated, as they are integral to the operation of virtually all electronic devices, from simple household appliances to complex computing systems. Given their pivotal role, the manufacturing of resistors is governed by stringent product standards that ensure quality, safety, and performance. This article aims to explore the various product standards that govern resistor factories, shedding light on their significance and the organizations that establish them.
II. Understanding Resistor Standards
Product standards in the context of resistors refer to the established criteria and specifications that manufacturers must adhere to during the production process. These standards are crucial for ensuring that resistors perform reliably and safely in their intended applications. They encompass various aspects, including electrical performance, safety, and environmental considerations.
International and national standards organizations play a vital role in developing and maintaining these standards. Their work ensures that resistors produced across different regions meet consistent quality benchmarks, facilitating global trade and enhancing consumer safety.
III. Key Standards Governing Resistor Manufacturing
A. International Electrotechnical Commission (IEC)
The International Electrotechnical Commission (IEC) is a leading organization that develops international standards for electrical and electronic technologies. One of the key standards relevant to resistors is IEC 60115, which outlines the general requirements for fixed resistors. This standard covers aspects such as resistance values, tolerances, temperature coefficients, and power ratings, ensuring that resistors meet specific performance criteria.
B. American National Standards Institute (ANSI)
In the United States, the American National Standards Institute (ANSI) plays a crucial role in setting standards for various industries, including electronics. ANSI standards applicable to resistor manufacturing include specifications for performance, safety, and testing methods. These standards help ensure that resistors produced in the U.S. meet the necessary quality and safety requirements.
C. Institute of Electrical and Electronics Engineers (IEEE)
The IEEE is another significant organization that contributes to the establishment of standards related to resistors. IEEE standards are particularly important in the context of electronic design, as they provide guidelines for the integration of resistors into complex circuits. These standards help engineers ensure that their designs are reliable and compliant with industry expectations.
D. Other Relevant Standards Organizations
Several other organizations contribute to the development of resistor standards, including:
International Organization for Standardization (ISO): ISO standards focus on quality management systems and environmental management, which can impact resistor manufacturing processes.
Underwriters Laboratories (UL): UL standards emphasize safety and performance, particularly in electrical components, including resistors.
European Committee for Electrotechnical Standardization (CENELEC): CENELEC develops standards for electrical and electronic products in Europe, ensuring compliance with regional regulations.
IV. Types of Resistor Standards
A. Performance Standards
Performance standards are critical for ensuring that resistors function as intended. Key aspects include:
1. **Tolerance Levels**: Tolerance indicates the permissible deviation from the nominal resistance value. Common tolerance levels for resistors range from ±1% to ±5%, with precision resistors offering tighter tolerances.
2. **Temperature Coefficient of Resistance (TCR)**: TCR measures how much a resistor's resistance changes with temperature. A lower TCR indicates better performance in varying temperature conditions.
3. **Power Rating and Derating**: The power rating specifies the maximum power a resistor can dissipate without failure. Derating involves operating the resistor below its maximum rating to enhance reliability and longevity.
B. Safety Standards
Safety standards are essential to prevent hazards associated with electrical components. Key safety considerations include:
1. **Electrical Safety Requirements**: Resistors must meet specific electrical safety criteria to prevent short circuits, overheating, and other electrical failures.
2. **Fire Safety and Flammability Testing**: Resistors are subjected to flammability tests to ensure they do not pose a fire risk under normal operating conditions.
C. Environmental Standards
Environmental standards address the ecological impact of resistor manufacturing and disposal. Important considerations include:
1. **RoHS Compliance**: The Restriction of Hazardous Substances (RoHS) directive limits the use of certain hazardous materials in electronic products, including resistors.
2. **REACH Compliance**: The Registration, Evaluation, Authorisation, and Restriction of Chemicals (REACH) regulation ensures that chemicals used in manufacturing are safe for human health and the environment.
3. **End-of-Life Disposal and Recycling Standards**: These standards promote responsible disposal and recycling of electronic components, reducing environmental impact.
V. Testing and Quality Assurance in Resistor Factories
A. Importance of Testing
Testing is a critical component of the manufacturing process, ensuring that resistors comply with established standards. Rigorous testing helps identify defects and ensures that products meet performance and safety requirements.
B. Common Testing Methods
1. **Electrical Testing**: This includes resistance measurement to verify that the resistor meets its specified value and tolerance.
2. **Environmental Testing**: Resistors undergo temperature cycling tests to assess their performance under varying thermal conditions.
3. **Mechanical Testing**: Vibration and shock tests evaluate the physical robustness of resistors, ensuring they can withstand real-world conditions.
C. Quality Assurance Processes
Quality assurance in resistor manufacturing involves several key processes:
1. **Incoming Material Inspection**: Raw materials are inspected to ensure they meet quality standards before production begins.
2. **In-Process Quality Control**: Continuous monitoring during the manufacturing process helps identify and rectify issues in real-time.
3. **Final Product Inspection and Testing**: Finished resistors undergo comprehensive testing to confirm compliance with all relevant standards before they are shipped to customers.
VI. Challenges in Meeting Product Standards
A. Technological Advancements
Rapid technological advancements can outpace existing standards, creating challenges for manufacturers. As new materials and designs emerge, standards must evolve to address these innovations.
B. Variability in Raw Materials
The quality and consistency of raw materials can significantly impact compliance with standards. Variability in material properties can lead to inconsistencies in resistor performance.
C. Globalization
As manufacturing becomes increasingly globalized, harmonizing standards across different regions is essential. Discrepancies in standards can create challenges for manufacturers operating in multiple markets.
D. Cost Implications
Adhering to stringent standards often involves additional costs related to testing, quality assurance, and compliance. Manufacturers must balance these costs with the need to produce high-quality products.
VII. Future Trends in Resistor Standards
A. Emerging Technologies
The rise of new technologies, such as IoT and AI, is influencing resistor design and standards. As electronic devices become more complex, standards will need to adapt to ensure compatibility and performance.
B. Sustainability
Sustainability is becoming a key focus in the electronics industry. Future standards are likely to emphasize environmentally friendly materials and manufacturing processes, promoting a circular economy.
C. Regulatory Changes
Anticipated changes in regulatory frameworks may lead to stricter compliance requirements. Manufacturers must stay informed about evolving regulations to ensure ongoing compliance.
VIII. Conclusion
In conclusion, product standards play a vital role in the manufacturing of resistors, ensuring quality, safety, and performance. Adherence to these standards is essential for manufacturers to meet customer expectations and regulatory requirements. As the electronics industry continues to evolve, the importance of robust product standards will only increase, shaping the future of resistor manufacturing and electronic design.
IX. References
- IEC 60115: Fixed Resistors for Use in Electronic Equipment
- ANSI Standards for Resistors
- IEEE Standards for Electronic Design
- RoHS Directive
- REACH Regulation
- ISO 9001: Quality Management Systems
- UL Standards for Electrical Components
This comprehensive overview of product standards in resistor factories highlights the critical role these standards play in ensuring the reliability and safety of electronic components. As technology advances and environmental considerations become more prominent, the landscape of resistor standards will continue to evolve, necessitating ongoing attention from manufacturers and engineers alike.