The Production Process of Mainstream Resistor 5
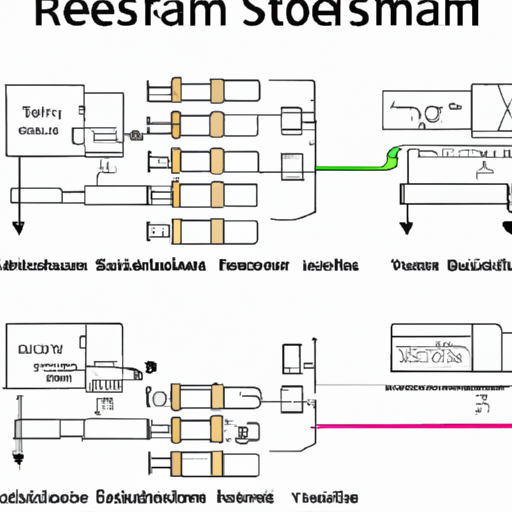
I. Introduction
A. Definition of Resistors
Resistors are passive electronic components that limit the flow of electric current in a circuit. They are essential for controlling voltage and current levels, ensuring that electronic devices operate safely and effectively.
B. Importance of Resistors in Electronic Circuits
In electronic circuits, resistors play a crucial role in protecting sensitive components, dividing voltages, and setting bias points for transistors. Without resistors, circuits would be prone to damage from excessive current, leading to failures in devices ranging from simple gadgets to complex machinery.
C. Overview of Mainstream Resistor 5
Among the various types of resistors, the Mainstream Resistor 5 stands out due to its reliability, precision, and versatility. It is widely used in consumer electronics, automotive applications, and industrial equipment, making it a staple in modern electronic design.
D. Purpose of the Document
This document aims to provide a comprehensive overview of the production process of Mainstream Resistor 5, detailing the materials, manufacturing steps, quality control measures, and environmental considerations involved in its creation.
II. Types of Resistors
A. Fixed Resistors
Fixed resistors have a constant resistance value and are the most common type used in electronic circuits. They are available in various resistance values and power ratings.
B. Variable Resistors
Variable resistors, such as potentiometers and rheostats, allow users to adjust resistance levels, making them ideal for applications like volume controls and tuning circuits.
C. Specialty Resistors
Specialty resistors are designed for specific applications, such as high-power resistors for power electronics or precision resistors for measurement devices.
D. Overview of Mainstream Resistor 5's Category
Mainstream Resistor 5 typically falls under the category of fixed resistors, known for its stability and accuracy. It is often used in applications requiring precise resistance values and minimal temperature drift.
III. Materials Used in Resistor Production
A. Conductive Materials
The choice of conductive material significantly impacts a resistor's performance.
1. **Carbon Composition**: These resistors are made from a mixture of carbon and a binding material. They are cost-effective but have higher noise levels and lower precision.
2. **Metal Film**: Metal film resistors are made by depositing a thin layer of metal onto a ceramic substrate. They offer better stability and lower noise, making them suitable for precision applications.
3. **Wirewound**: Wirewound resistors consist of a wire wound around a core. They can handle high power and are often used in high-performance applications.
B. Insulating Materials
Insulating materials are crucial for ensuring the resistor's performance and longevity.
1. **Epoxy Resins**: These are used for encapsulating resistors, providing protection against moisture and mechanical stress.
2. **Ceramic**: Ceramic materials are often used as substrates due to their excellent thermal stability and electrical insulation properties.
C. Substrates and Packaging Materials
The choice of substrate and packaging materials affects the resistor's thermal performance and reliability. Common materials include glass, plastic, and metal for packaging, ensuring durability during transport and use.
IV. The Production Process of Mainstream Resistor 5
A. Design and Engineering
1. Specifications and Standards
The production of Mainstream Resistor 5 begins with defining specifications based on industry standards. This includes resistance values, tolerance levels, and power ratings.
2. Simulation and Prototyping
Engineers use computer-aided design (CAD) software to simulate the resistor's performance under various conditions. Prototyping allows for testing and refinement before mass production.
B. Material Preparation
1. Sourcing Raw Materials
Manufacturers source high-quality raw materials from trusted suppliers. This step is critical to ensure the final product meets performance standards.
2. Quality Control of Materials
Incoming materials undergo rigorous quality control checks to verify their properties and ensure they meet the required specifications.
C. Manufacturing Steps
1. Resistor Element Fabrication
The core of the resistor is fabricated using various techniques:
Carbon Film Deposition: A thin layer of carbon is deposited onto a substrate, forming the resistive element.
Metal Film Sputtering: A metal layer is sputtered onto the substrate, creating a precise resistive path.
Wirewound Techniques: A wire is wound around a ceramic core, forming the resistive element.
2. Trimming and Tolerance Adjustment
After fabrication, resistors are trimmed to achieve the desired resistance value. This process may involve laser trimming or mechanical cutting to ensure precise tolerance levels.
3. Encapsulation and Coating
The resistive elements are encapsulated in insulating materials, such as epoxy or ceramic, to protect them from environmental factors. A coating is applied to enhance durability and provide additional insulation.
D. Assembly and Packaging
1. Mounting on Substrates
Resistors are mounted onto printed circuit boards (PCBs) or other substrates, ready for integration into electronic devices.
2. Final Inspection and Testing
Each batch of resistors undergoes final inspection and testing to ensure they meet quality standards. This includes checking resistance values, power ratings, and physical integrity.
3. Packaging for Distribution
Once tested, resistors are packaged in protective materials to prevent damage during transport. Packaging is designed to be both functional and informative, providing essential details about the product.
V. Quality Control and Testing
A. Importance of Quality Control
Quality control is vital in resistor production to ensure reliability and performance. Defective resistors can lead to circuit failures, impacting the overall functionality of electronic devices.
B. Testing Methods
1. Electrical Testing
Electrical tests measure resistance values, tolerance levels, and power ratings to ensure compliance with specifications.
2. Environmental Testing
Resistors undergo environmental testing to assess their performance under various conditions, including temperature fluctuations, humidity, and mechanical stress.
3. Reliability Testing
Reliability tests simulate long-term usage to identify potential failure modes and ensure the resistor's longevity.
C. Compliance with Industry Standards
Manufacturers adhere to industry standards, such as ISO and IEC, to ensure their products meet global quality and safety requirements.
VI. Environmental Considerations
A. Sustainable Practices in Resistor Production
Manufacturers are increasingly adopting sustainable practices, such as using eco-friendly materials and reducing waste during production.
B. Recycling and Disposal of Resistors
Proper recycling and disposal methods are essential to minimize environmental impact. Many manufacturers offer take-back programs for old resistors.
C. Regulatory Compliance
Compliance with environmental regulations, such as RoHS (Restriction of Hazardous Substances), ensures that resistors are free from harmful materials.
VII. Conclusion
A. Summary of the Production Process
The production process of Mainstream Resistor 5 involves meticulous design, material selection, and manufacturing techniques. From sourcing raw materials to final testing, each step is crucial for ensuring high-quality resistors.
B. Future Trends in Resistor Manufacturing
As technology advances, the demand for more precise and reliable resistors will grow. Innovations in materials and manufacturing processes will likely lead to the development of even more efficient resistors.
C. The Role of Resistors in Advancing Technology
Resistors remain a fundamental component in electronic circuits, playing a vital role in the advancement of technology. As electronic devices become more complex, the importance of high-quality resistors will only increase.
VIII. References
A. Academic Journals
- Journal of Electronic Materials
- IEEE Transactions on Components, Packaging and Manufacturing Technology
B. Industry Reports
- Resistor Market Analysis Report
- Global Electronic Components Market Trends
C. Manufacturer Guidelines
- Manufacturer specifications and quality assurance documents
This blog post provides a detailed exploration of the production process of Mainstream Resistor 5, highlighting the importance of each step in ensuring the quality and reliability of this essential electronic component.
The Production Process of Mainstream Resistor 5
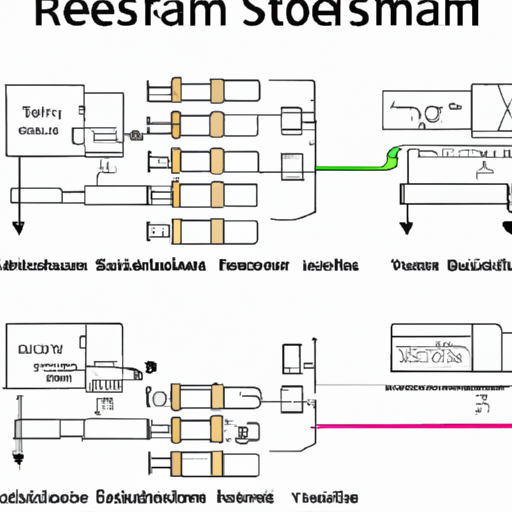
I. Introduction
A. Definition of Resistors
Resistors are passive electronic components that limit the flow of electric current in a circuit. They are essential for controlling voltage and current levels, ensuring that electronic devices operate safely and effectively.
B. Importance of Resistors in Electronic Circuits
In electronic circuits, resistors play a crucial role in protecting sensitive components, dividing voltages, and setting bias points for transistors. Without resistors, circuits would be prone to damage from excessive current, leading to failures in devices ranging from simple gadgets to complex machinery.
C. Overview of Mainstream Resistor 5
Among the various types of resistors, the Mainstream Resistor 5 stands out due to its reliability, precision, and versatility. It is widely used in consumer electronics, automotive applications, and industrial equipment, making it a staple in modern electronic design.
D. Purpose of the Document
This document aims to provide a comprehensive overview of the production process of Mainstream Resistor 5, detailing the materials, manufacturing steps, quality control measures, and environmental considerations involved in its creation.
II. Types of Resistors
A. Fixed Resistors
Fixed resistors have a constant resistance value and are the most common type used in electronic circuits. They are available in various resistance values and power ratings.
B. Variable Resistors
Variable resistors, such as potentiometers and rheostats, allow users to adjust resistance levels, making them ideal for applications like volume controls and tuning circuits.
C. Specialty Resistors
Specialty resistors are designed for specific applications, such as high-power resistors for power electronics or precision resistors for measurement devices.
D. Overview of Mainstream Resistor 5's Category
Mainstream Resistor 5 typically falls under the category of fixed resistors, known for its stability and accuracy. It is often used in applications requiring precise resistance values and minimal temperature drift.
III. Materials Used in Resistor Production
A. Conductive Materials
The choice of conductive material significantly impacts a resistor's performance.
1. **Carbon Composition**: These resistors are made from a mixture of carbon and a binding material. They are cost-effective but have higher noise levels and lower precision.
2. **Metal Film**: Metal film resistors are made by depositing a thin layer of metal onto a ceramic substrate. They offer better stability and lower noise, making them suitable for precision applications.
3. **Wirewound**: Wirewound resistors consist of a wire wound around a core. They can handle high power and are often used in high-performance applications.
B. Insulating Materials
Insulating materials are crucial for ensuring the resistor's performance and longevity.
1. **Epoxy Resins**: These are used for encapsulating resistors, providing protection against moisture and mechanical stress.
2. **Ceramic**: Ceramic materials are often used as substrates due to their excellent thermal stability and electrical insulation properties.
C. Substrates and Packaging Materials
The choice of substrate and packaging materials affects the resistor's thermal performance and reliability. Common materials include glass, plastic, and metal for packaging, ensuring durability during transport and use.
IV. The Production Process of Mainstream Resistor 5
A. Design and Engineering
1. Specifications and Standards
The production of Mainstream Resistor 5 begins with defining specifications based on industry standards. This includes resistance values, tolerance levels, and power ratings.
2. Simulation and Prototyping
Engineers use computer-aided design (CAD) software to simulate the resistor's performance under various conditions. Prototyping allows for testing and refinement before mass production.
B. Material Preparation
1. Sourcing Raw Materials
Manufacturers source high-quality raw materials from trusted suppliers. This step is critical to ensure the final product meets performance standards.
2. Quality Control of Materials
Incoming materials undergo rigorous quality control checks to verify their properties and ensure they meet the required specifications.
C. Manufacturing Steps
1. Resistor Element Fabrication
The core of the resistor is fabricated using various techniques:
Carbon Film Deposition: A thin layer of carbon is deposited onto a substrate, forming the resistive element.
Metal Film Sputtering: A metal layer is sputtered onto the substrate, creating a precise resistive path.
Wirewound Techniques: A wire is wound around a ceramic core, forming the resistive element.
2. Trimming and Tolerance Adjustment
After fabrication, resistors are trimmed to achieve the desired resistance value. This process may involve laser trimming or mechanical cutting to ensure precise tolerance levels.
3. Encapsulation and Coating
The resistive elements are encapsulated in insulating materials, such as epoxy or ceramic, to protect them from environmental factors. A coating is applied to enhance durability and provide additional insulation.
D. Assembly and Packaging
1. Mounting on Substrates
Resistors are mounted onto printed circuit boards (PCBs) or other substrates, ready for integration into electronic devices.
2. Final Inspection and Testing
Each batch of resistors undergoes final inspection and testing to ensure they meet quality standards. This includes checking resistance values, power ratings, and physical integrity.
3. Packaging for Distribution
Once tested, resistors are packaged in protective materials to prevent damage during transport. Packaging is designed to be both functional and informative, providing essential details about the product.
V. Quality Control and Testing
A. Importance of Quality Control
Quality control is vital in resistor production to ensure reliability and performance. Defective resistors can lead to circuit failures, impacting the overall functionality of electronic devices.
B. Testing Methods
1. Electrical Testing
Electrical tests measure resistance values, tolerance levels, and power ratings to ensure compliance with specifications.
2. Environmental Testing
Resistors undergo environmental testing to assess their performance under various conditions, including temperature fluctuations, humidity, and mechanical stress.
3. Reliability Testing
Reliability tests simulate long-term usage to identify potential failure modes and ensure the resistor's longevity.
C. Compliance with Industry Standards
Manufacturers adhere to industry standards, such as ISO and IEC, to ensure their products meet global quality and safety requirements.
VI. Environmental Considerations
A. Sustainable Practices in Resistor Production
Manufacturers are increasingly adopting sustainable practices, such as using eco-friendly materials and reducing waste during production.
B. Recycling and Disposal of Resistors
Proper recycling and disposal methods are essential to minimize environmental impact. Many manufacturers offer take-back programs for old resistors.
C. Regulatory Compliance
Compliance with environmental regulations, such as RoHS (Restriction of Hazardous Substances), ensures that resistors are free from harmful materials.
VII. Conclusion
A. Summary of the Production Process
The production process of Mainstream Resistor 5 involves meticulous design, material selection, and manufacturing techniques. From sourcing raw materials to final testing, each step is crucial for ensuring high-quality resistors.
B. Future Trends in Resistor Manufacturing
As technology advances, the demand for more precise and reliable resistors will grow. Innovations in materials and manufacturing processes will likely lead to the development of even more efficient resistors.
C. The Role of Resistors in Advancing Technology
Resistors remain a fundamental component in electronic circuits, playing a vital role in the advancement of technology. As electronic devices become more complex, the importance of high-quality resistors will only increase.
VIII. References
A. Academic Journals
- Journal of Electronic Materials
- IEEE Transactions on Components, Packaging and Manufacturing Technology
B. Industry Reports
- Resistor Market Analysis Report
- Global Electronic Components Market Trends
C. Manufacturer Guidelines
- Manufacturer specifications and quality assurance documents
This blog post provides a detailed exploration of the production process of Mainstream Resistor 5, highlighting the importance of each step in ensuring the quality and reliability of this essential electronic component.